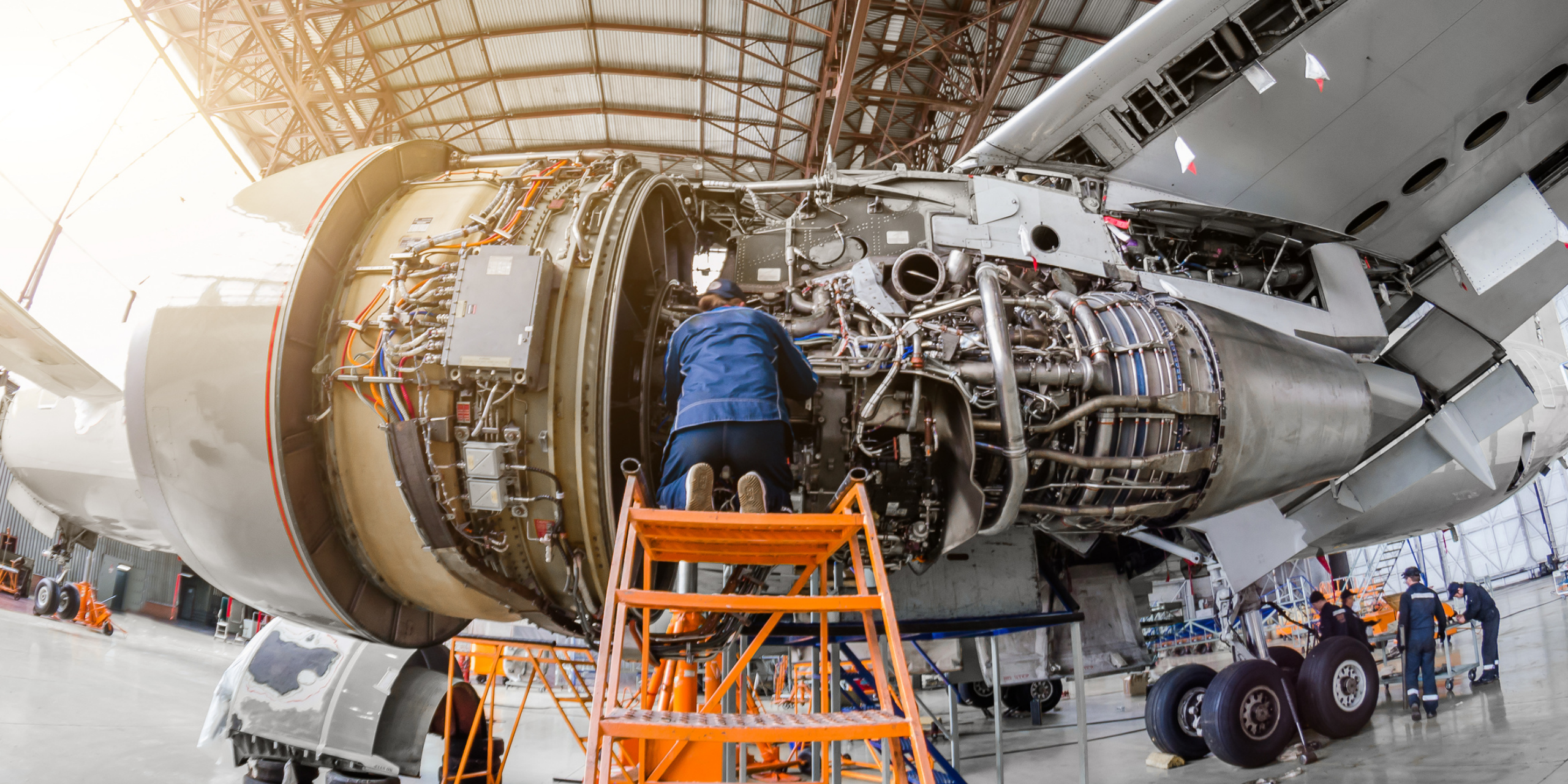
Top 7 Aircraft Redelivery Pain Points
Author: Lee Smith, Senior Technical Manager at flydocs
With airlines now predominantly leasing aircraft as opposed to purchasing them as in the past, the need to ensure the aircraft is operated within the terms of the lease conditions has never been more important to both lessors and lessees. The lease will contain details of what is expected of the lessee when redelivering the aircraft at the end of its operation.
There are many challenges that present themselves whilst preparing the aircraft for its redelivery. While there are some lease returns that go without a glitch, there will be others that will prove to be painful, taking up countless hours of resources, which could lead to a delayed return with penalties possibly running into millions of dollars.
Below, are seven common pain points that, if unmanaged, could lead to problematic aircraft redeliveries.
1. Consistency of technical records
During the lifetime of an aircraft (including aircraft that have been leased by previous operators), tens of thousands of pages of data are generated in the form of technical logs, pilot reports, work orders, dirty fingerprints, modifications, repairs, etc. Most of these will be required to be collated and presented to the lessors for review as part of the aircraft redelivery process, which can be one of the most laborious tasks in the entire process.
As a lot of these records are created in some manual form (physically or digitally), errors and omissions will invariably creep in during the lease period. This can be particularly challenging if a good process isn’t set up to audit the records in advance of the aircraft’s return. This is because making amendments to documents many months or years after the event can be time-consuming, especially if trying to work with third-party repair agencies and MROs where support may be complex.
An upfront approach to avoiding issues related to records is to conduct an audit several months prior to the lessor’s review, to assess any significant issues between the condition of the records versus the lease return conditions. This will provide the lessee with additional time to identify and carry out any relevant remedial action, and if necessary, a discussion with the lessor to agree on the best course of action.
2. Managing components installed in returning aircraft
Each lease will specify within its return conditions what is expected from any components changed during the aircraft’s operation with the lessee.
Much of the time it is expected that no components should be fitted to the aircraft that exceed 100%/110% of the age of the airframe, although other rules may apply depending on the lessor.
It is important that the lessee has an awareness of the age of the aircraft whilst replacing components, especially leading up to its lease return. Good component planning and management allow parts to be replaced sooner if access and downtime are available and minimise the risk of last-minute component changes. Without this, it could lead to unforeseen additional project costs, due to the unknown component price, its lead time, and available personnel to carry out the replacement, all during the final maintenance input.
3. Unscheduled repairs
Any aircraft damage or repairs with poorly completed maintenance records can create potentially major issues during its lease return, especially for any damage that has been missed or unrecorded.
This can include:
- Not following approved data
- A lack of damage information
- Sign-off data
- Missing supporting documents supplied by the OEM, etc.
All of this, if unmanaged, could easily result in any concerned repairs requiring reidentification and/or rework. This, of course, runs the risk of delays to the aircraft redelivery due to the time required to complete the repairs, and lead time for any materials.
Having a robust digital asset and component management system to manage any repairs during the life of the aircraft is important, as it would show all damage reported, including documents associated with each individual repair. This also allows ample time to review each of these for any corrections required in the lead-up to the aircraft return, and alongside a physical inspection, during suitable downtime, should ensure that any rework or issues are planned well in advance of the final maintenance input.
4. Modification Management
The need to provide detailed technical records to reflect the status of any avionic or cabin interior modifications and supplemental type certificate mods (STCs), can be a time-consuming and complex task, if not correctly managed during the time the aircraft is in operation with the lessee.
Modification documents are required to provide clear details of their intent along with further information, including installation of any follow-up maintenance requirements and instructions on how to return the aircraft to its original configuration, if necessary. It is also important to prove that the modifications were carried out in accordance with approved aviation authority body data (e.g. FAA, EASA).
Any errors identified with modifications embodied on an aircraft could again result in issues during the lease return process, as further documentation may be required, clarification of a mod status, physical inspections, or at worst, full removal of a modification that the lessor deems not required during its redelivery. This can be a very timely and expensive part of the process, if not controlled correctly.
A timely review of the installed modifications prior to the aircraft’s return will allow lessees to identify issues that may arise.
5. Burn certification
The materials used in the interior and cargo compartments of an aircraft must meet certain regulatory flammability requirements. Regulations require materials to be fire resistant, which would enable enough time for passengers to exit an aircraft in the event of a fire. This is of importance to items such as seat foams, cushions, dress fabrics, curtains, carpets, galley flooring, cargo liners & panels, etc. Items replaced during the aircraft’s operation, which are not OEM-specific, must adhere to the regulations and relevant documents conforming to the materials’ flammability compliance must be provided.
Without closely monitoring the burn certification/flammability reports for any relevant items changed on the aircraft, collating this data in the lead-up to a lease return can be a very time-consuming task. This could result in the need to carry out physical inspections of the aircraft interior and then searching through the aircraft records to find the relevant documentation, without which the items may require replacement before redelivery.
6. Lack of support and resources
The level of effort that is required from technical experts during the lease return process should not be underestimated, as a well-supported process is important in ensuring lessors and lessees have the opportunity to address the wide range of issues that arise during aircraft redelivery.
Managing aircraft during its lease term with a dedicated team and an effective asset management system ensures fewer resources are required during mid-term inspections and the final lease return process. Being aware of potential problems in advance of the return date allows any additional maintenance to be pre-planned whilst minimising potential unknown issues. This can also be helpful when working with lessors during the transition, as awareness of potential problems can be discussed in advance, allowing both sides to come to a reasonable conclusion.
A proactive approach to continuous asset management is always advised during the lease period to ensure as smooth a redelivery as possible.
7. Lack of understanding of the aircraft lease conditions
It’s very common for lessees when receiving a shiny new leased aircraft, to not consider the implications for five or ten years down the line when it’s time to hand it back to the lessor.
An understanding of the lease conditions from the early days of operation is essential, as lease agreements are broad and detailed but aren’t always completely clear in their interpretations. This could be due to a lack of staff experience, differing opinions, cultures, languages, or even perceptions. There can be occasions where a lessee simply believes that keeping the aircraft airworthy is enough to meet a lessor’s requirements when it’s time for the aircraft redelivery, but without an awareness of the details contained within the lease, there are many pitfalls the lessee could encounter, which could amount to hundreds of thousands of dollars in penalties or late fees.
Having an experienced asset transition team supporting the lessee’s organisation, and which has awareness and knowledge of leasing contracts can be invaluable, as they can review the lease and liaise with the lessor regarding any queries or concerns in good time. That team can also present a lease contract interpretation that breaks down the key points of importance to be aware of during the lease period. This helps to ensure relevant stakeholders within the lessee’s organisation understand their obligations during both the time the aircraft is in operation through to the return process, from records preparation, physical inspections, final engine, and APU borescopes, through to demo flights and final acceptance.
Conclusion
With the right, team, digital asset management system, experience, knowledge and support, the challenge to redeliver an aircraft on time and within a budget doesn’t have to be so daunting.
The Technical Services team at flydocs can support your organisation throughout the whole transition process and can help you mitigate the seven common challenges described in this article, while completely eliminating some of these.
Get in touch with us to start simplifying the aircraft redelivery process for your teams.