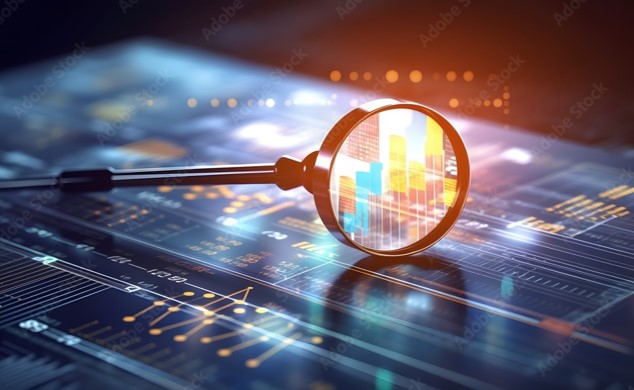
Things to consider before taking on a used aircraft
Author:
Lee Smith
Technical Sales Manager
With significant delays in new aircraft from OEM production lines that may not ease for the next two years, many airlines are looking at used aircraft as a viable option for fleet expansion.
While this can be a cost-effective strategy, acquiring a used aircraft comes with its own unique challenges. It’s essential to carefully assess whether the aircraft fits your operational needs and integrates seamlessly with your existing fleet.
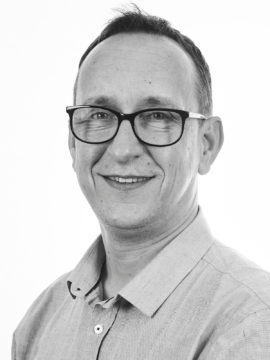
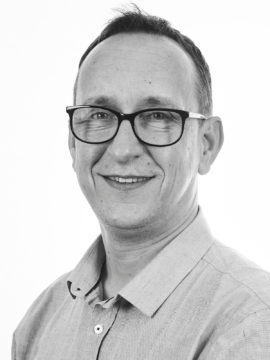
Here, we’ll explore the top things to consider before taking on a used aircraft into an operation.
1. Understand the aircraft’s maintenance history
Key steps: Reviewing the maintenance records is crucial to understanding how well the aircraft has been maintained and whether any recurring issues could impact future operations.
Checklist:
- Review all heavy maintenance events.
- Investigate any modifications, especially STCs (Supplemental Type Certificates).
- Assess compliance with Airworthiness Directives (ADs) and Service Bulletins (SBs).
- Check for deferred maintenance or carry-forward items that may affect operational readiness.
- Investigate any previous incidents or accidents involving the aircraft & assemblies to confirm that any necessary corrective actions been properly documented to ensure continued airworthiness.
- Assess the life remaining for engines, landing gear and APUs until their next overhaul or performance restoration
Pro tip: Use a document management platform to streamline record reviews and ensure alignment with the Maintenance Planning Document (MPD) and your airline’s Approved Maintenance Program (AMP).
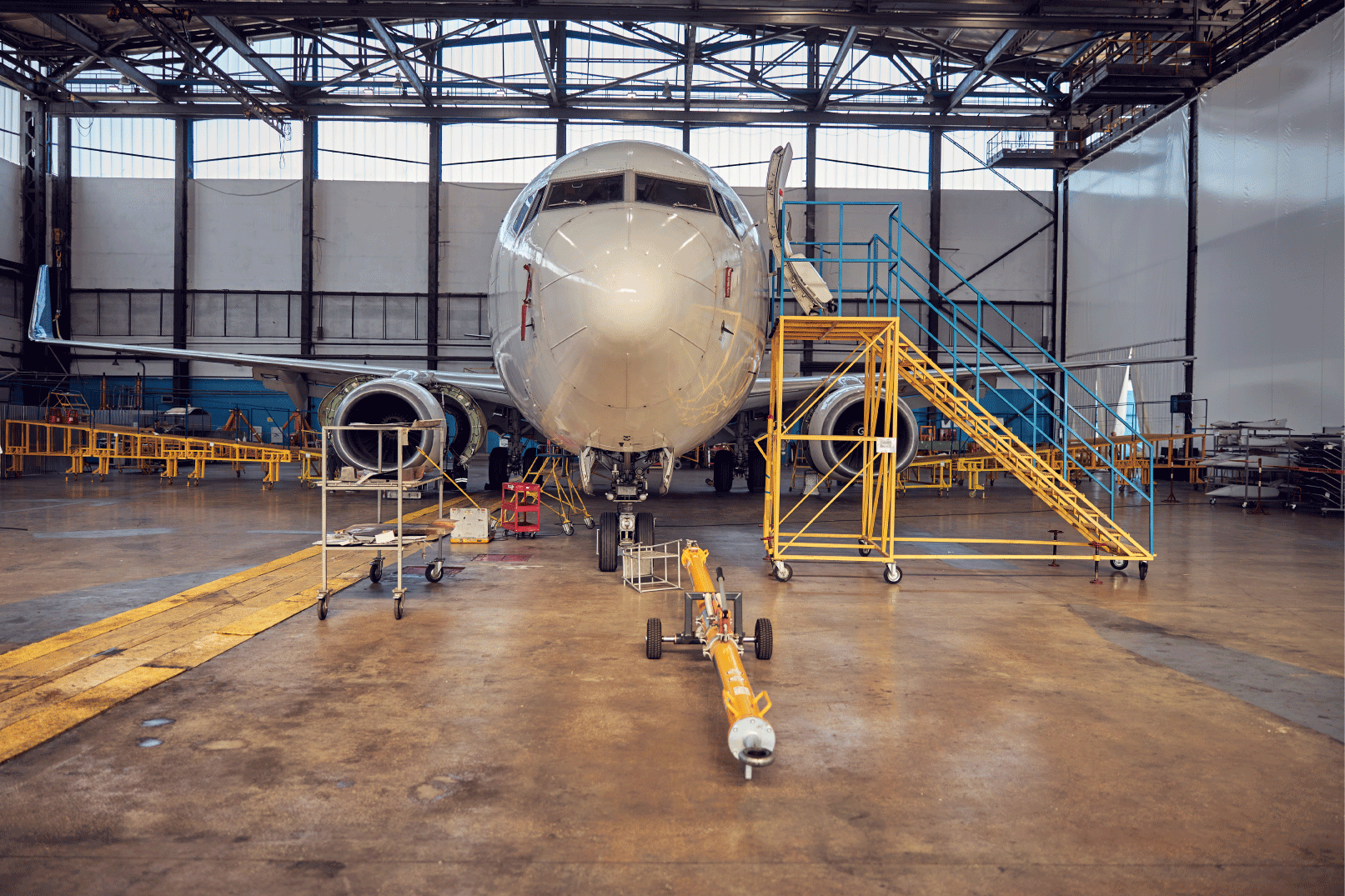
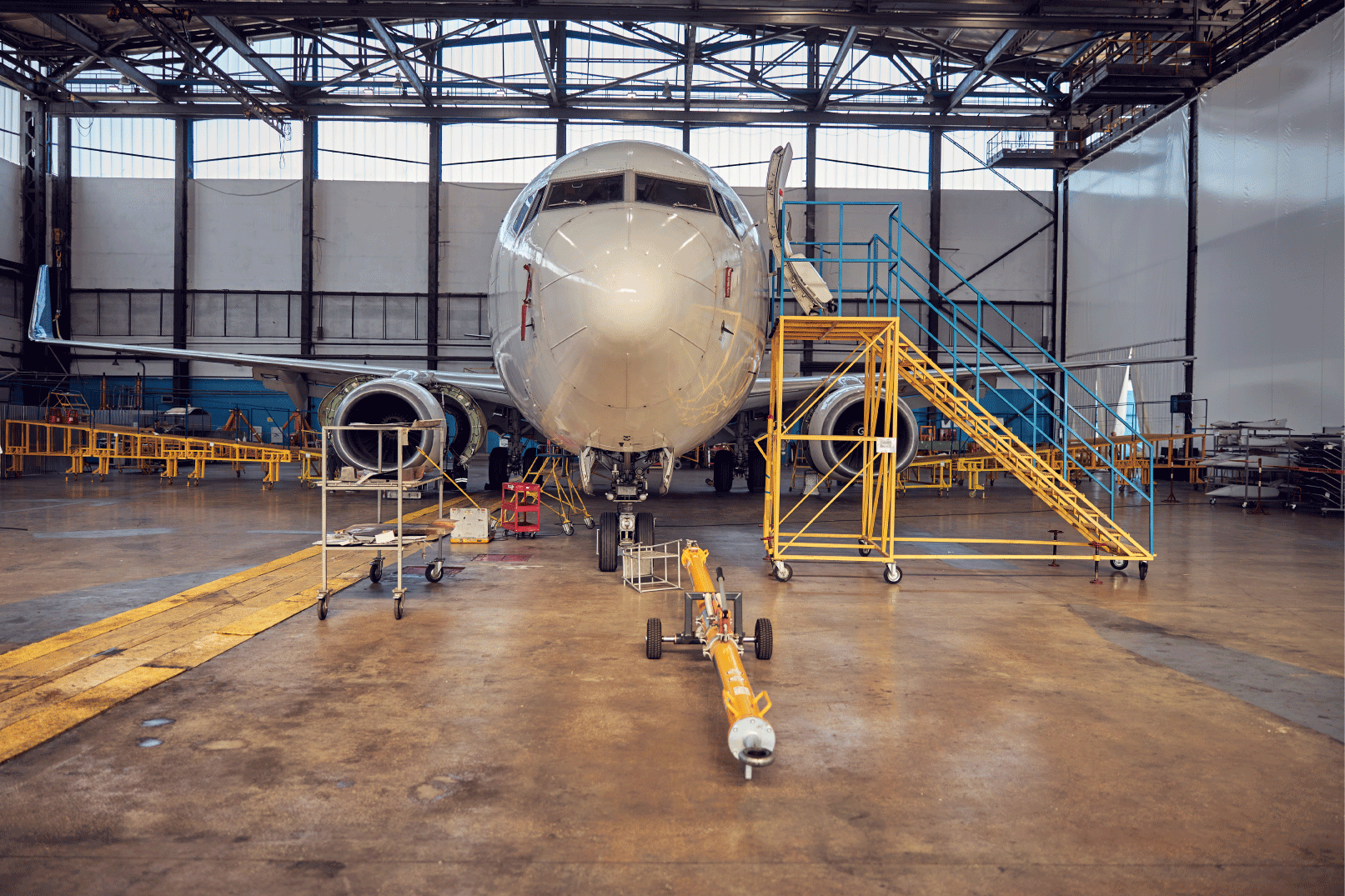
2. Evaluate airframe and engine condition
Airframe inspections: Assess the airframe for signs of corrosion, fatigue, or damage. Structural integrity is crucial, as even minor damage in high-stress areas can impact safety and long-term maintenance costs.
Engine review: The engine’s remaining lifecycle and performance are key factors. An engine with significant life left reduces immediate costs but consider long-term overhaul expenses and the remaining cycles.
Inspection points:
- Last heavy maintenance check (e.g., C or D check).
- Detailed borescope inspections on engines.
- Fuel system and fuel tank condition, particularly for older models.
- Physical condition of key components such as landing gear, APUs, thrust reversers, and cowls.
Pro tip: Work with your engine OEM or maintenance provider to assess engine health data, including trending reports on critical metrics like oil consumption and vibration.
3. Assess regulatory compliance
Aircraft must meet specific regulatory standards for your region and operational requirements. Compliance with certification, ADs, and environmental regulations is essential.
Considerations:
- Does the aircraft meet with noise and emissions standards required in your operating regions?
- If intended for long-haul routes, is it certified for Extended Twin Operations (ETOPS)?
- Ensure that replaced components, modifications, or repairs align with your local regulatory requirements. For instance, approvals from one regulatory authority may not automatically be accepted by another.
- Identify any PMA (Parts Manufacturer Approval) components or DER (Designated Engineering Representative) repairs that may need further validation.
Pro tip: Use detailed compliance software to confirm adherence to all applicable ADs and requirements, including any recent regulatory changes to keep your fleet up-to-date and operating smoothly.
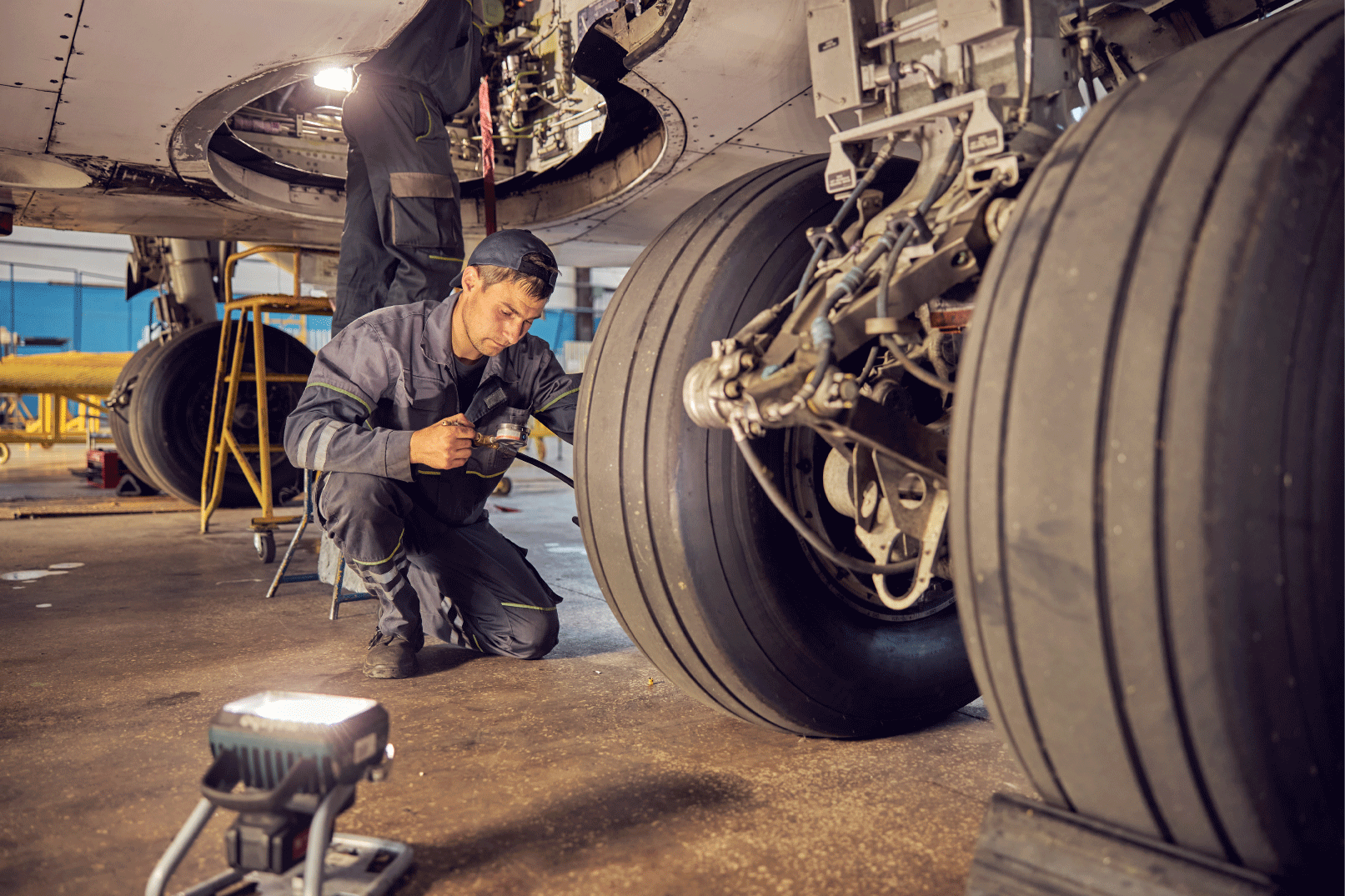
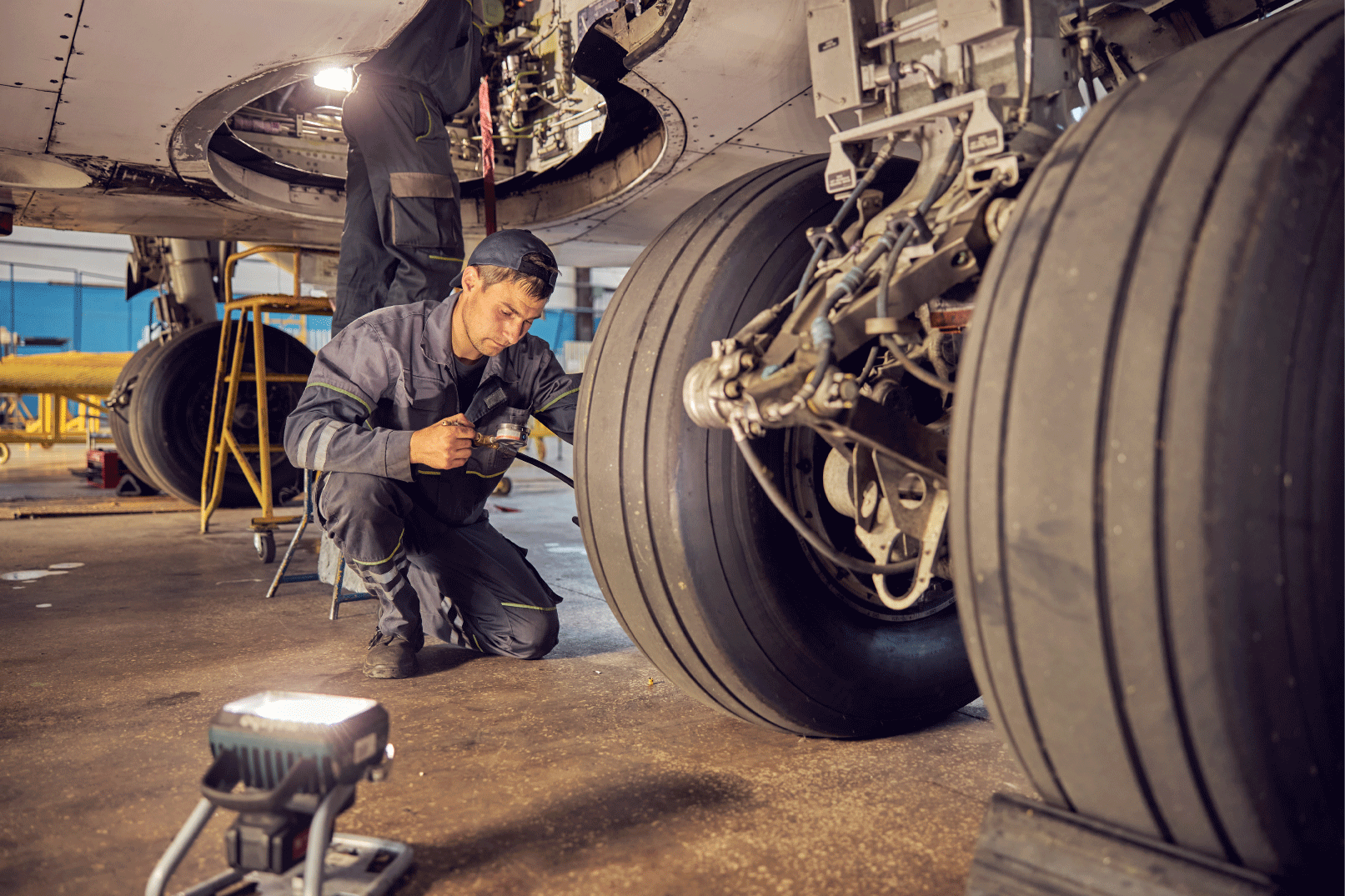
4. Conduct a fleet commonality review
When considering fleet expansion through the acquisition of used aircraft, conducting a commonality review is essential to ensure the addition aligns with your operational standards and integrates seamlessly with your existing fleet. By evaluating technical compatibility, you can minimise operational disruptions and maintain consistency in maintenance and operations
Key aspects:
- Evaluate component interchangeability, maintenance schedule alignment, and parts stocking.
- Review crew training requirements and any unique technical demands of the aircraft.
- Confirm that the IFE (In-Flight Entertainment) systems, seating configuration, and amenities fit your brand and service model.
Pro tip: A comprehensive commonality review enables informed decisions based on operational and engineering data, supporting a seamless transition into operations.
5. Review cabin and configuration compatibility
Cabin configuration impacts passenger experience and operational efficiency. Ensuring compatibility with your brand and operational model is key.
Key aspects:
- Evaluate seat layout and potential retrofitting needs.
- Assess in-flight entertainment (IFE) and connectivity systems.
- Review lavatory and galley layouts, as modifications to these areas can be costly.
- Verify that burn certifications for interior materials comply with local regulations.
Pro tip: Consider any brand alignment issues if the aircraft configuration differs from your airline’s standard.
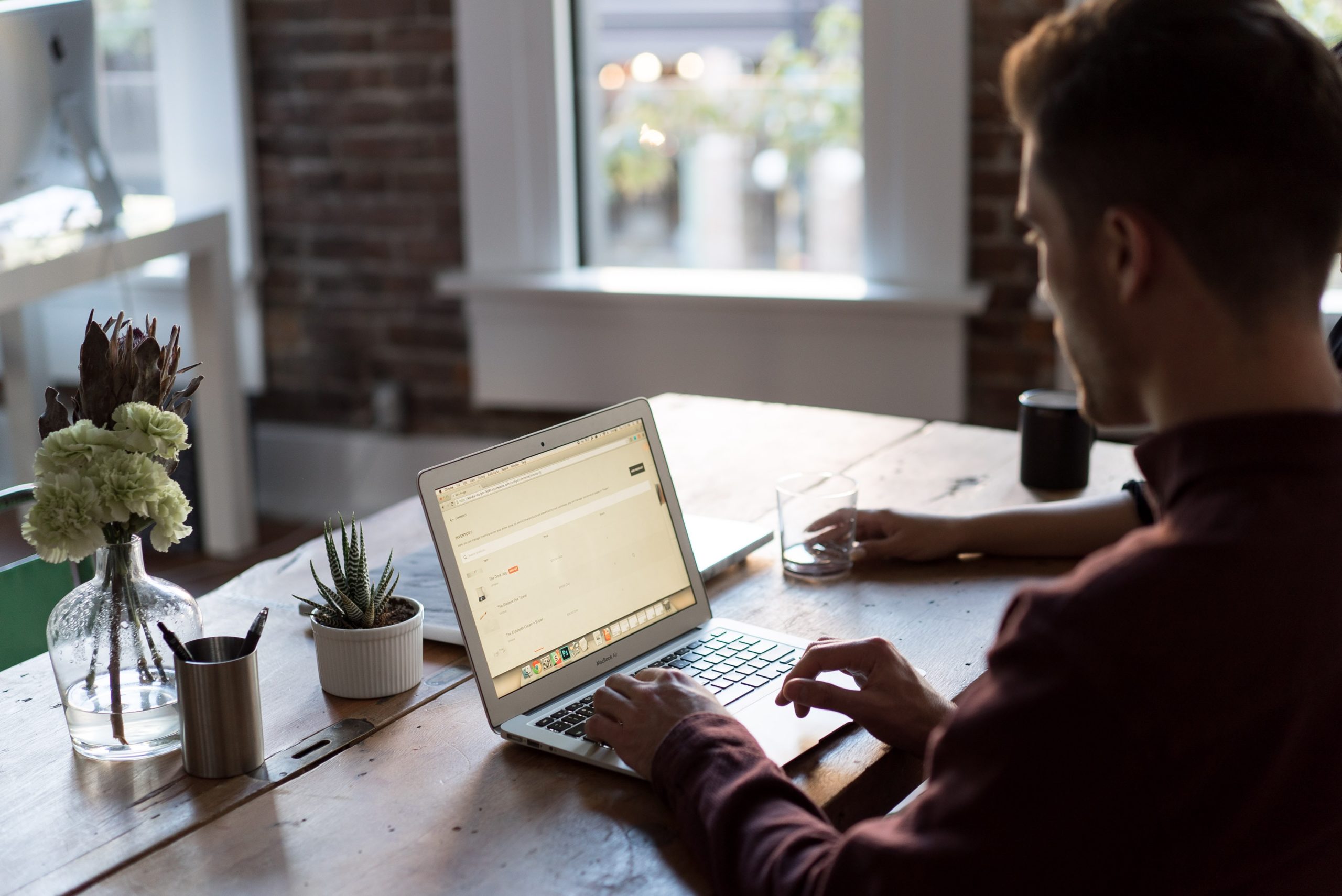
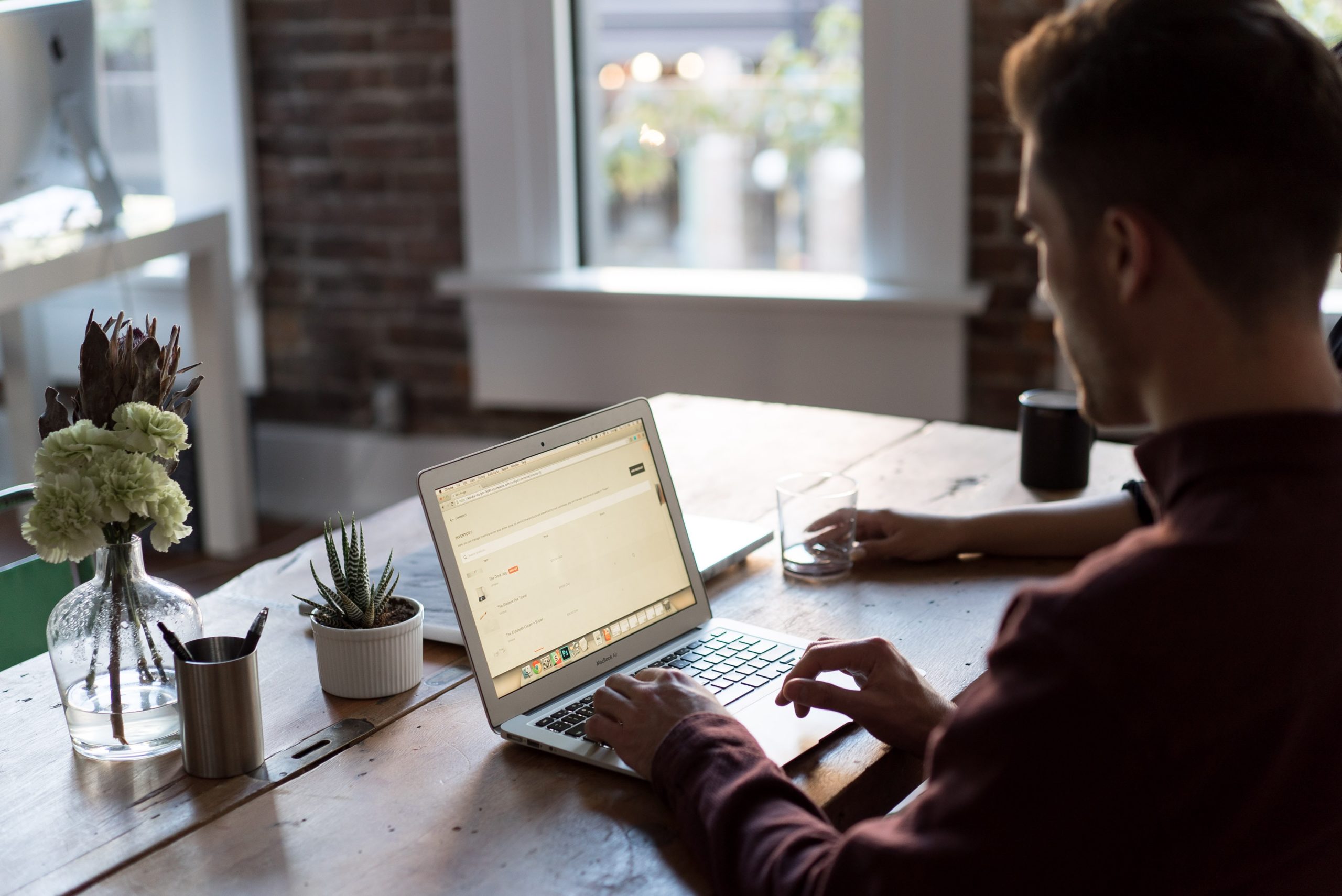
6. Examine records for lease return conditions
Leased aircraft often come with specific return conditions that, if unmet, can lead to high costs. Ensuring these conditions were met by the previous operator can save significant time and expense.
Checklist:
- Confirm back-to-birth records, including traceability of parts & components.
- Look for any “grey areas” in lease terms that could result in penalties.
- Review any upcoming maintenance events that may fall on your operating budget soon after acquisition.
- Confirm the availability and completeness of all digital & physical record inventory boxes as applicable.
Pro tip: Document discrepancies early on and, if needed, negotiate for remedial work or compensation from the lessor or seller.
7. Plan for integration and operational readiness
A seamless induction process minimises downtime and ensures the aircraft can enter service quickly. Consider how this aircraft will integrate into your operational and maintenance frameworks.
Preparation steps:
- Ensure maintenance schedule alignment and part availability.
- Update IT and asset management systems with the aircraft’s records.
- Develop a training plan for engineering and flight crews if the aircraft type differs from existing models.
Pro tip: Hold an induction meeting with stakeholders across engineering, operations, and finance to outline the acquisition timeline and address potential challenges.
Conclusion
In today’s environment of delayed OEM production, acquiring a used aircraft can be a smart way to meet fleet expansion goals. However, a successful acquisition depends on thorough technical evaluations, regulatory compliance and seamless operational integration.
By leveraging tools like document management systems, compliance trackers and project management tools, airlines can simplify the complexities of used aircraft acquisition and maximise operational readiness. A well-executed plan ensures the new addition to your fleet is both cost-effective and aligned with your strategic goals.
Did you know we can support with a variety of technical projects, including pre-purchase/sales inspections and fleet transition management? Get in touch to chat to our team about how we can help you.