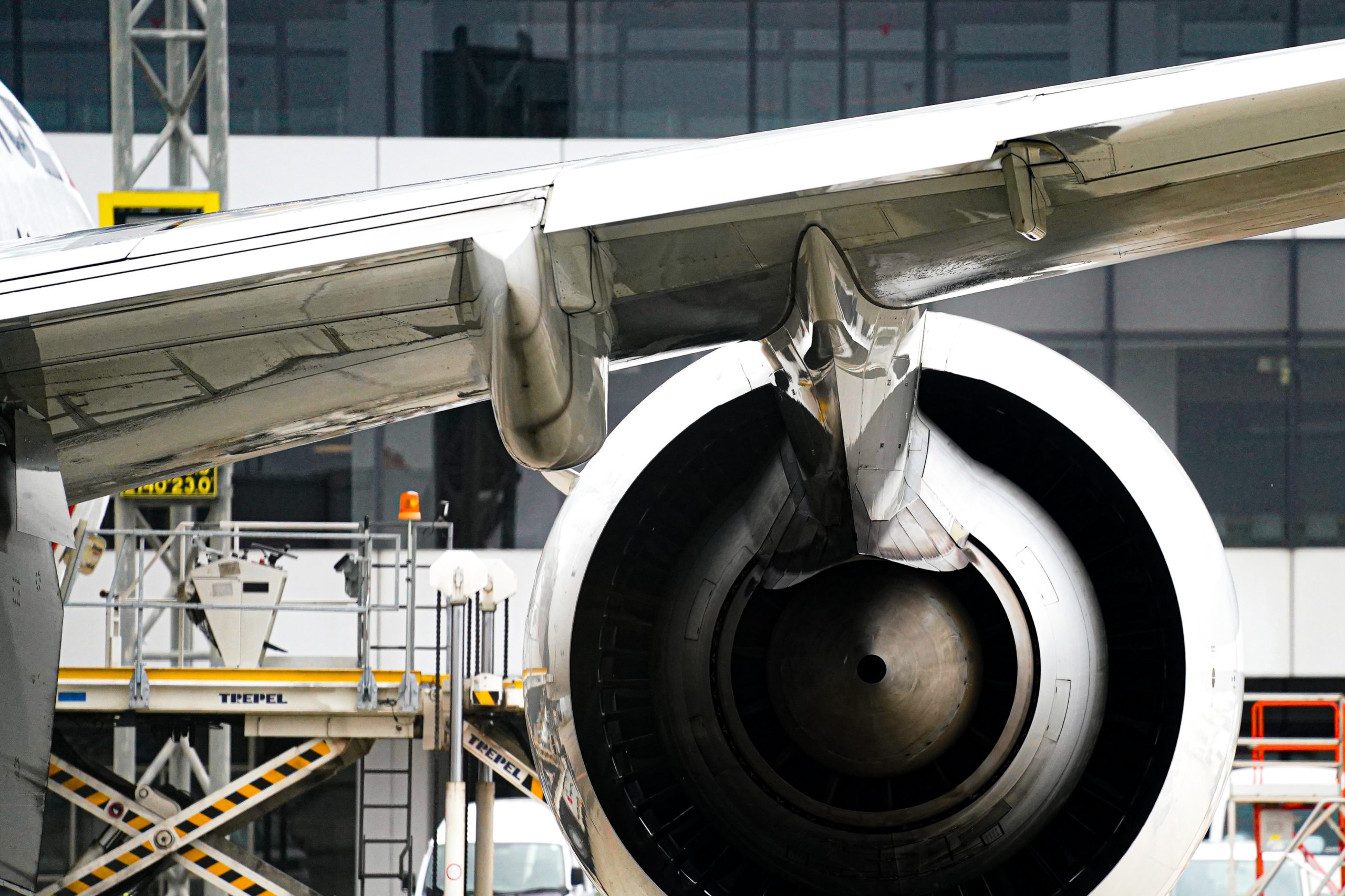
Navigating interior burn certification in aircraft transitions
Aircraft transitions bring a host of unique challenges, with interior burn certification emerging as a critical aspect for lessors, buyers and operators alike.
This article explores the intricacies of the certification process, highlighting the key components, strategies for compliance, and approaches to resolving common disputes.
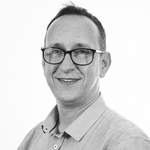
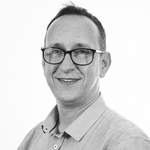
Lee Smith, Senior Technical Manager, flydocs
Explaining interior burn certification
Interior burn certification ensures compliance with stringent flammability standards set by the Federal Aviation Regulations (FAR) 25.853 and the European Aviation Safety Agency (EASA) CS-25. This process evaluates the flammability of materials used within the aircraft’s interior to meet strict fire safety requirements, safeguarding passengers and crew.
Components subject to interior burn certification
The scope of interior burn certification extends to a wide range of cabin components, including:
- Seat covers and cushions
- Sidewalls and ceiling panels
- Carpets
- Galley and lavatory non-textile flooring (NTF)
- Overhead stowage compartments (hat racks)
- Curtains and dividers
These items, found across passenger cabins and flight deck areas, must meet the required safety standards before the aircraft can transition to its next phase of operation.
Steps to ensure compliance with interior burn certification requirements
Ensuring compliance with interior burn certification requires a thorough, step-by-step approach:
Verify original manufacturer’s documentation: Begin by checking the aircraft’s delivery documents for original flammability reports provided by the manufacturer.
Secure applicable approvals and certifications: For replacement parts installed per the Illustrated Parts Catalogue (IPC), ensure the availability of Authorised Release Certificates (ARCs) and supporting flammability reports.
Perform a physical inspection: When documentation is incomplete, carry out a physical inspection of the relevant interior components. Confirm part numbers, serial numbers, and batch details. Compile a matrix report to identify data gaps and flag components that may need further action or replacement
Obtain test results for modifications: For parts installed through modifications or Supplemental Type Certificates (STCs), ensure the availability of approved test reports, mod approvals and ARCs that align with EASA/FAA standards.
Addressing common disputes in interior burn certification and how to address them
Despite best efforts, challenges may arise during the certification process. Common issues include:
- Missing or incomplete ARCs and burn test reports
- Discrepancies between installed parts and those listed in the IPC
- Last-minute sourcing of replacement items, often leading to additional costs or delays
To mitigate these risks, operators may consider performing detailed inspections several months in advance. Early identification of gaps allows time to gather missing documentation, plan for potential replacements, and avoid unexpected penalties.
Conclusion
Interior burn certification can be a crucial factor of regulatory compliance during aircraft transitions. By proactively verifying documentation and resolving potential disputes early, operators can streamline the transition process whilst maintaining regulatory compliance.